Beyond Taste: How Magnet Calibration & Magnet Measuring Impacts Food Safety
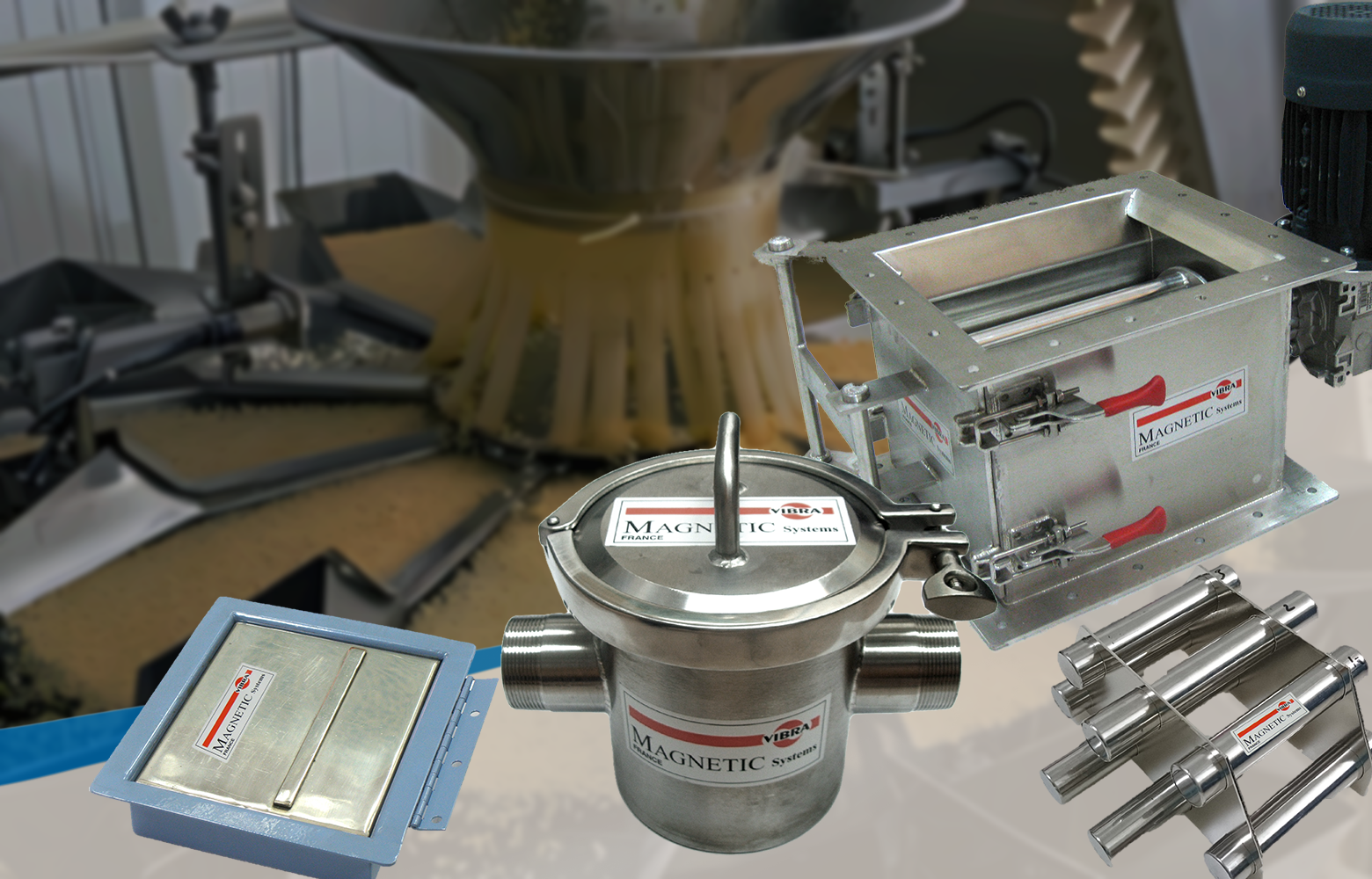
While the importance of magnet calibration and magnet measuring may not be top of mind, understanding its practical implications can significantly impact your food processing operations. In this article, we'll explore the practical aspects of magnet calibration and magnet measuring, including its purpose, the different types of magnets used in business food processing, how magnet strength affects food quality, the risks of inadequate calibration and measuring, the advantages of precise calibration and measuring, the calibration and measuring process itself, and best practices for businesses.
What Is Magnet calibration/Magnet measuring?
Put simply, magnet calibration/magnet measuring is the process of measuring the magnetic strength of magnets used in food processing. This measurement ensures the magnets effectively capture and remove metal contaminants from food products.
The Purpose of Calibration/Measuring in the Food Industry
In the food industry, calibration/measuring serves as a critical quality control measure. Manufacturers can effectively prevent metal contaminants, such as iron, from entering the food production process by ensuring that magnets are calibrated/measured to the right strength. This is vital for maintaining food safety and protecting consumers from potential health hazards.
The Different Types of Magnets Used in Food Processing
Magnets come in various forms, each designed for specific applications in food processing. The three primary types of magnets used in this industry are:
- Ferrite Magnets. These are commonly used in food processing for basic magnetic separation due to their cost-effectiveness and reliable performance.
- Neodymium Magnets. Known for their exceptional magnetic strength, neodymium magnets are used when high-intensity magnetic separation is required, such as in the extraction of fine metal contaminants.
- Samarium Cobalt Magnets. These magnets are chosen for their high-temperature resistance and durability in harsh food processing environments.
How Magnet Strength Affects Food Quality
The strength of magnets plays a pivotal role in determining the efficiency of metal separation in the food processing industry. When properly calibrated, magnets can attract and remove metal contaminants, essential for maintaining food quality and safety.
The magnetic strength of the magnets used in food processing equipment must be carefully matched to the application. If the magnets are too weak, they may fail to capture metal contaminants effectively. On the other hand, if the magnets are too strong, they may lead to the undesirable capture of non-metallic elements, resulting in food wastage and increased production costs.
The Dangers of Inadequate Calibration/Measuring
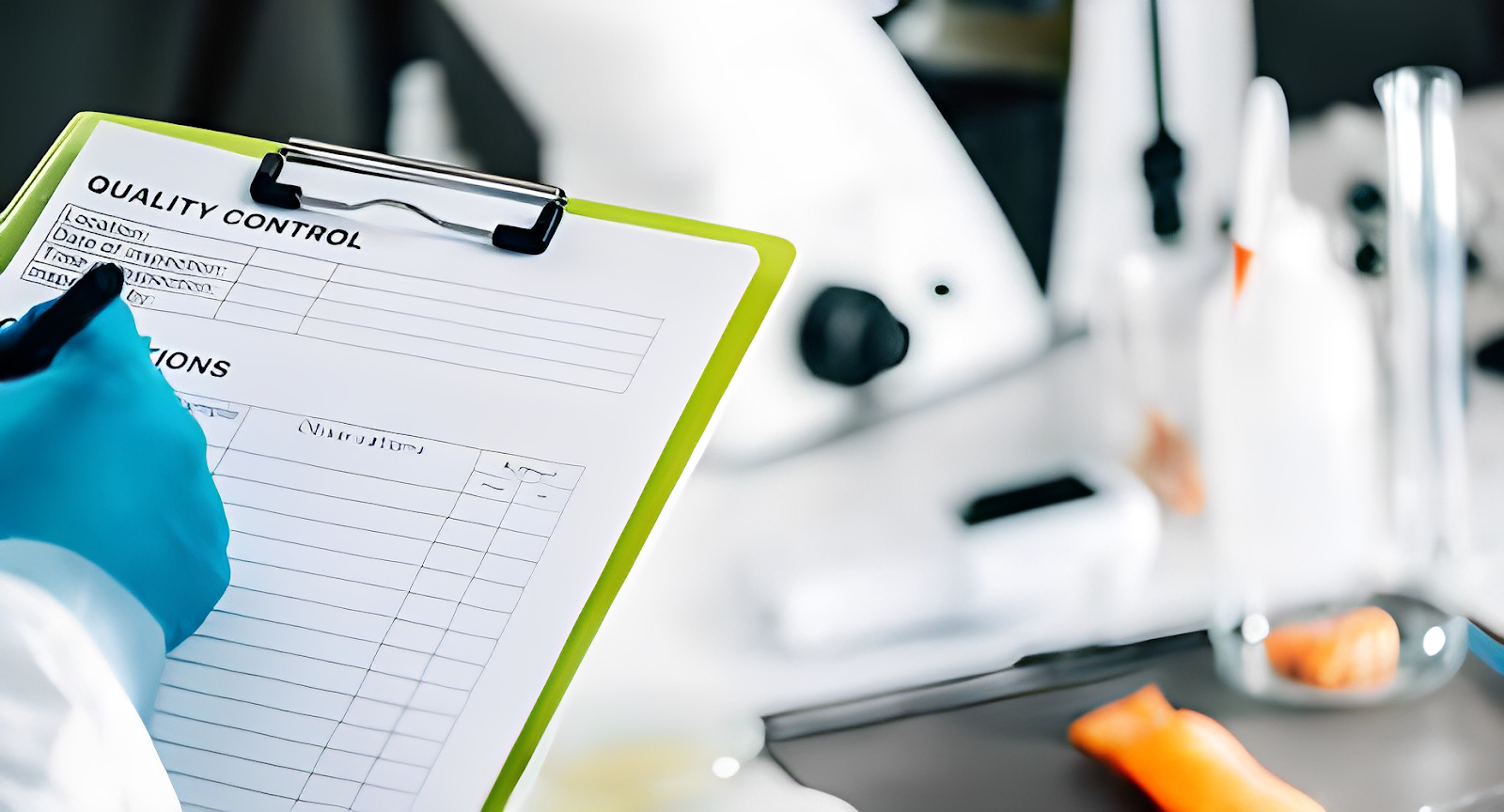
Inadequate magnet calibration/magnet measuring in the food processing industry can lead to a cascade of problems, with potential risks to food safety, quality control, regulatory compliance, and cost implications.
Potential Risks to Food Safety
One of the most significant dangers of inadequate magnet calibration/magnet measuring is the risk of metal contamination in food products. Consuming food contaminated with metal particles can pose severe health risks to consumers, potentially leading to injuries or even fatalities. This risk alone emphasises the critical importance of properly calibrated/measured magnets in food processing.
Quality Control and Regulatory Compliance
Inadequate calibration/measuring can also result in a lack of control over food quality. This can lead to inconsistencies in the final product, negatively impacting the reputation of food manufacturers and potentially causing product recalls.
Moreover, various regulatory bodies and food safety standards, such as the Hazard Analysis and Critical Control Points (HACCP) system, mandate the use of properly calibrated/measured magnets in food processing. Failure to comply with these standards can lead to legal consequences and damage to a company's reputation.
Cost Implications of Inaccurate Calibration/Measuring
Inaccurate calibration/measuring can also have financial repercussions. When magnets are not calibrated correctly, manufacturers may experience increased waste due to rejected batches and higher production costs to rectify the issues. This can significantly impact a company's bottom line.
The Benefits of Accurate Calibration/Measuring
Accurate magnet calibration/magnet measuring brings a host of benefits to the food processing industry, ranging from enhanced food safety and quality to compliance with food regulations and cost-efficiency.
Enhanced Food Safety and Quality
Properly calibrated/measured magnets effectively remove metal contaminants from production, ensuring the final food product is safe for consumption. This, in turn, enhances food quality and reduces the risk of recalls and consumer complaints.
Compliance with Food Regulations and Standards
Accurate calibration/measuring is a fundamental requirement to comply with food safety regulations and industry standards. Staying in compliance not only avoids legal issues but also builds trust among consumers, retailers, and regulatory bodies.
Cost-Efficiency in Food Processing
Accurate calibration/measuring reduces the risk of product recalls and minimises waste. This results in cost savings and streamlined production processes. Food manufacturers can achieve long-term cost-efficiency and enhanced profitability by investing in proper magnet calibration/magnet measuring.
How The Calibration/Measuring Process of Magnets is Done
The calibration/measuring process involves measuring the magnetic strength of magnets. Professionals with expertise in magnet technology typically carry out this process. They use specialised equipment and procedures to ensure precise calibration/measuring. Calibration/Measuring is not a one-time task; it must be repeated periodically to maintain the magnet's effectiveness over time.
Best Practices in Magnet Calibration / Magnet Measuring
For food manufacturers looking to maintain the integrity of their products and ensure consumer safety, here are some best practices in magnet calibration/magnet measuring:
Proper Handling and Maintenance of Magnets
Regular maintenance is crucial to ensure the longevity and performance of magnets. This includes cleaning, checking for signs of wear, and ensuring magnets are properly stored to prevent damage.
Routine Inspection and Cleaning
Routine inspection and cleaning are essential to prevent contaminants from building up on magnets and affecting their performance. Inspecting magnets for any damage and cleaning them when necessary helps maintain their efficiency.
Calibration/Measuring Schedule and Documentation
Having a well-documented calibration/measuring schedule is critical to ensure that magnets are consistently calibrated/measured at the required strength. Regular calibration/measuring and detailed records of the process are essential for quality control and regulatory compliance.
Get the Right Magnet Testing Service in Malaysia
The role of magnet measuring and calibration in food safety cannot be overstated. It's not just about maintaining the taste of your products; it's about ensuring the safety and well-being of your consumers. This is why, when it comes to ensuring that your magnets are calibrated/measured correctly and your food production process is free from metal contaminants, it's essential to partner with experts who understand the intricacies of magnet calibration/magnet measuring.
In Malaysia,
Sematic Magnet offers top-notch magnet testing services that can help you maintain the highest levels of food safety, quality, and regulatory compliance - precision matters, and Sematic Magnet is here to ensure that you get it right.
Contact our magnet specialist today for expert guidance.
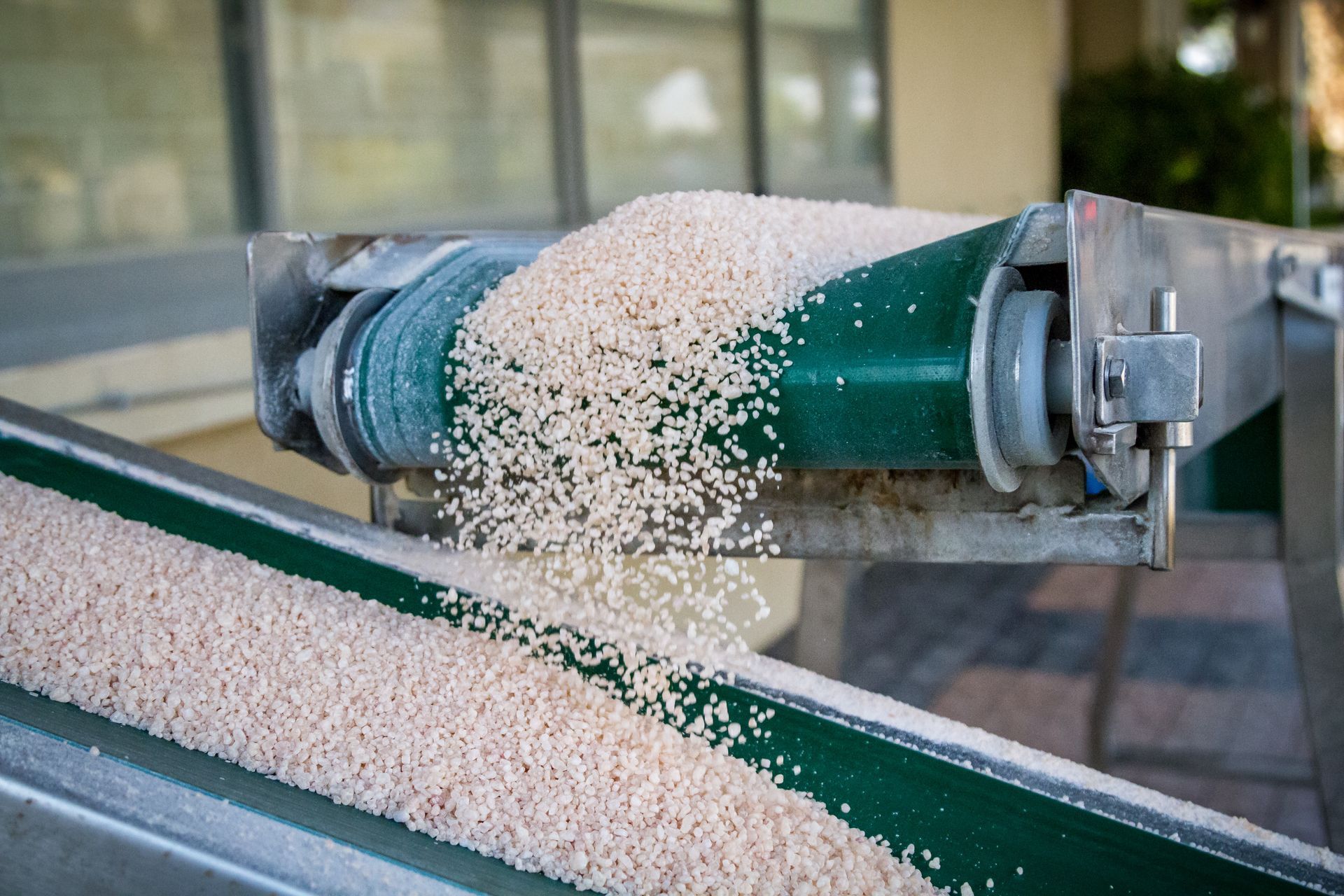